Application
Port Terminals
- Coal Handling:
At coal-dedicated terminals, ship loaders play a vital role. Large volumes of coal are transported from mines to port stockyards via rail, road, or belt conveyors, and then loaded onto bulk carriers using ship loaders. For example, in major coal hub ports like Qinhuangdao, ship loaders handle thousands of tons daily, shipping coal to power plants and steel mills both domestically and internationally. - Ore Loading:
Ship loaders are essential for loading both metallic ores (such as iron, copper, and bauxite) and non-metallic ores (like limestone and silica sand). After mining and processing, the ore is delivered to ports, where ship loaders transfer it to vessels based on required flow rates and loading patterns. - Grain Transfer:
At grain terminals, ship loaders are used to load wheat, corn, rice, and other grains. Grains are transported from silos to the ship loader via conveyors, which then evenly distributes the grain into the ship’s hold, according to the vessel’s capacity and loading requirements.
Bulk Logistics Industry
- Chemical Raw Materials:
In chemical ports, ship loaders are used for loading powdered, granular, or lump chemical raw materials safely and efficiently. - Building Material Loading:
Ship loaders are also used for bulk construction materials such as cement, sand, and gravel. At ports near material production facilities, these loaders transfer construction materials to vessels, supplying coastal and inland construction projects. For example, in coastal cities, ship loaders at construction material terminals supply large quantities of raw materials for infrastructure and real estate development.
Mining & Metallurgy Industry (Private Terminals)
- Mining Terminals:
At mine-owned port facilities, ship loaders directly load extracted ores onto vessels, reducing intermediate transport steps and increasing efficiency. For instance, some large mines in Australia use in-house port ship loaders to ship ore to overseas markets or domestic processing plants. - Metallurgical Raw Material Loading:
Metallurgical plants such as steel and aluminum factories often require large quantities of ores and additives. These materials are often transported via waterways, with ship loaders at plant-affiliated ports handling bulk loading. Additionally, ship loaders can be used to transport recyclable byproducts like slag for further use (e.g., in construction materials).
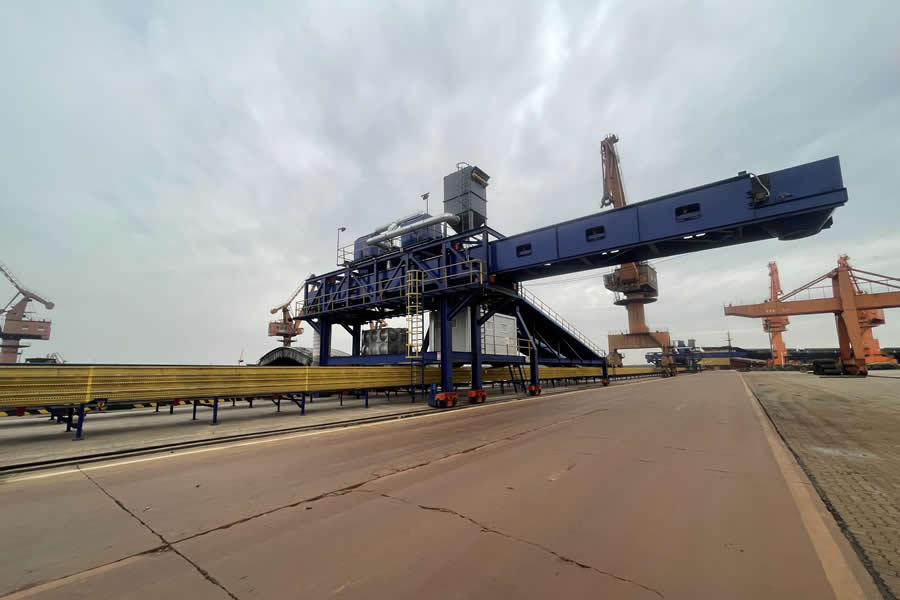
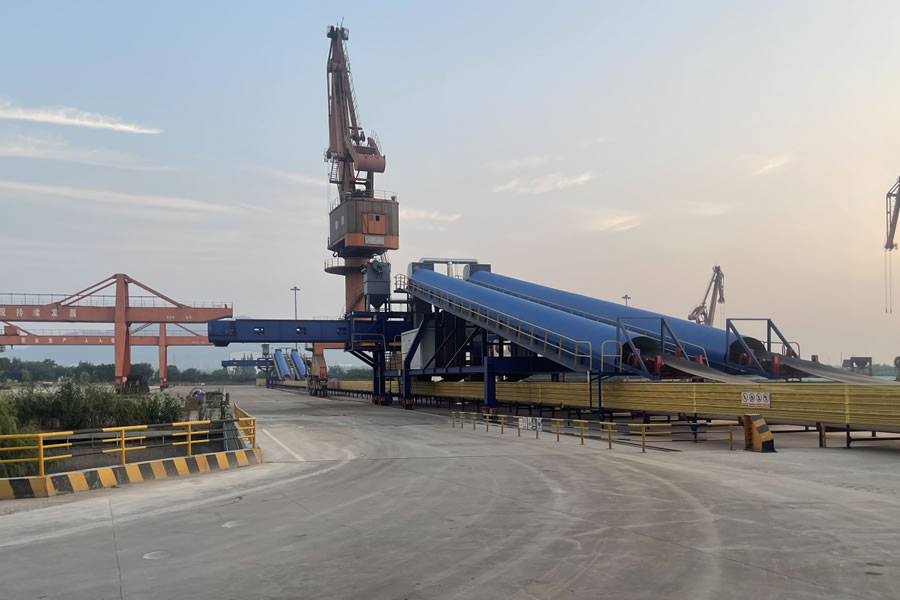
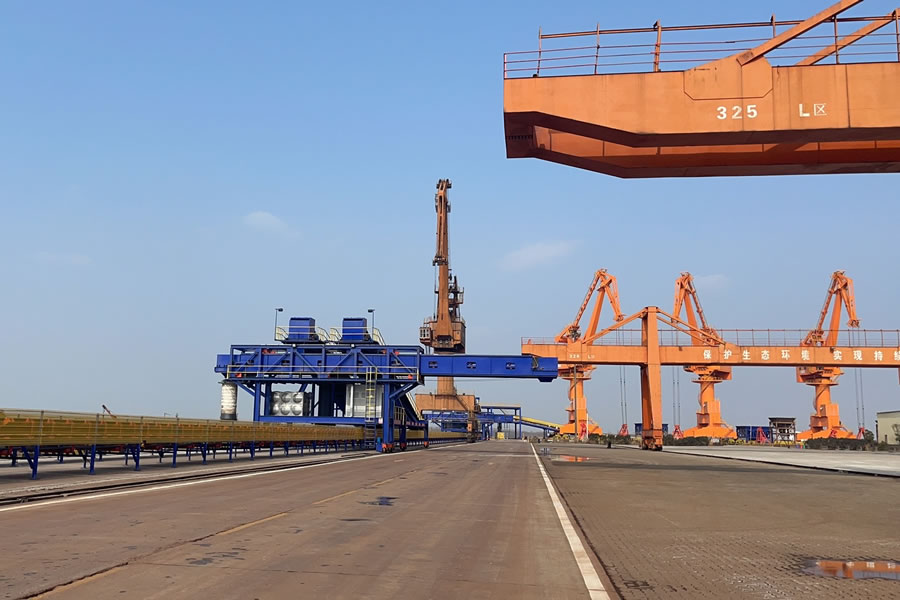
Advantages
Loading Capacity
- High Throughput:
Ship loaders offer extremely high material handling rates, with loading capacities reaching several thousand tons per hour. Equipped with large belt conveyors, they transport material efficiently from stockyards to ship holds. At large coal terminals, a single ship loader can handle up to 10,000 tons per hour, significantly improving port productivity and reducing vessel turnaround time. - Continuous Operation:
Designed for uninterrupted long-hour operation, ship loaders run steadily through extended shifts. For example, during ore loading, the equipment can operate continuously for hours or days, supporting high-volume tasks unless halted for maintenance.
Precise Loading Control
- Flow Rate Regulation:
Ship loaders feature variable frequency drives (VFD) and other systems that allow precise control of material flow. Flow speed can be adjusted based on vessel requirements and material properties. For example, during grain loading, the flow can be kept steady to avoid uneven distribution or product damage. For high-precision materials like chemical powders, exact volume control ensures consistent batch loading. - Positioning Accuracy:
The discharge chute of the ship loader can move within the ship hold to ensure even distribution. Equipped with laser rangefinders, encoders, and automation systems, it precisely positions the discharge point to fill all sections of the hold. This helps avoid excessive concentration of material in one area and ensures the vessel remains balanced during loading.
Superior Adaptability
- Material Versatility:
Ship loaders can handle various bulk materials, including lumpy ores, fine powders, and granules. Adjustments in belt speed, discharge method, and sealing can accommodate different material characteristics such as particle size, density, and flowability. For instance, slower belt speeds are used for coarse ores to avoid spillage, while sealed conveyors are preferred for fine cement to reduce dust. - Compatibility with Different Vessel Sizes:
Ship loaders can serve a wide range of vessel sizes, from small inland barges to large ocean-going bulk carriers. Parameters such as boom length and discharge height are adjustable to match the vessel dimensions. For example, when loading Panamax-class bulkers, the loader can extend its boom to reach optimal height and coverage; for smaller barges, it adjusts angle and flow rate accordingly. - High Environmental Performance:
Ship loaders are equipped with systems to reduce dust and spillage during operation. For powder materials, enclosed conveying and discharging systems minimize airborne dust. Dust collectors are installed at key transfer points and discharge areas. Structural design and sealing prevent material leakage, ensuring compliance with environmental standards and protecting port surroundings.
Technical Specifications
Ship Loader | ||
Hopper Volume | 0.5 m³- 5 m³ | Customizable |
Loading Capacity | 100 – 3000 t/h (customizable) | |
Applicable Materials | Coal, ore, sand, gravel, grain, and other bulk cargo | |
Belt Width | 0.8 m – 2 m | |
Control Systems | PLC and DCS systems | |
Discharge Chute Diameter | 0.5 m – 1.5 m | |
Power | 400 kW | |
Operation Modes | Manual and automatic | |
Luffing Angle | –30° to +45° | |
Conveyor Belt Speed | 1.8 m/s – 4 m/s |