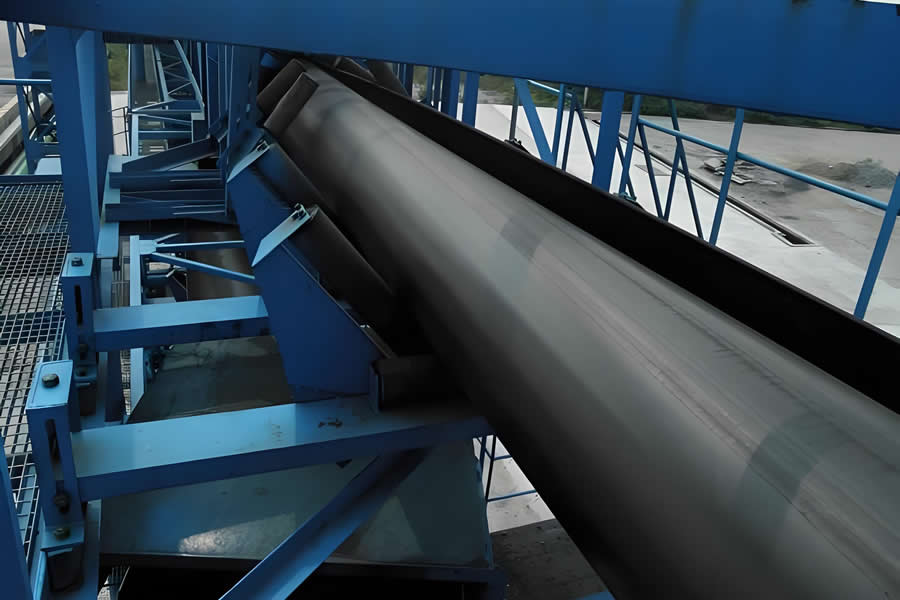
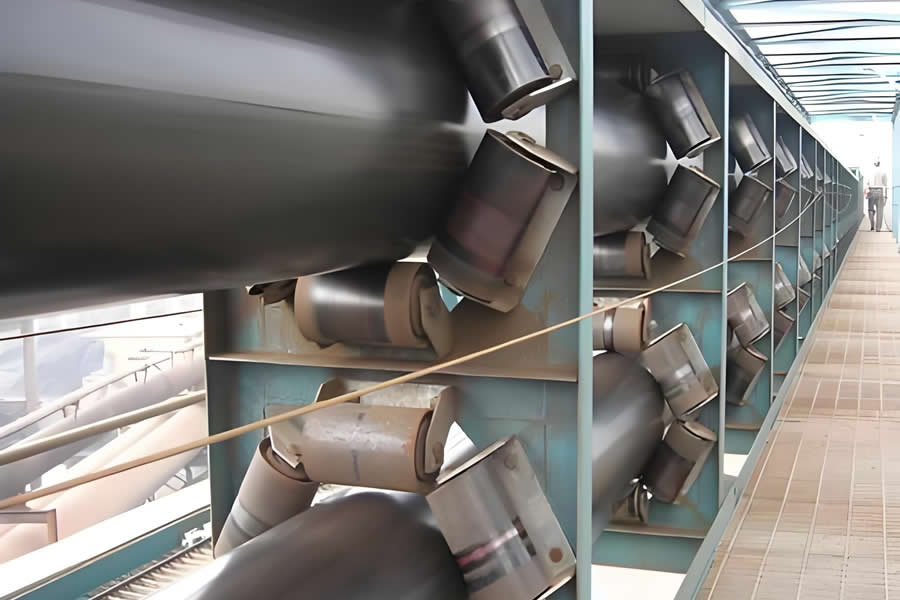
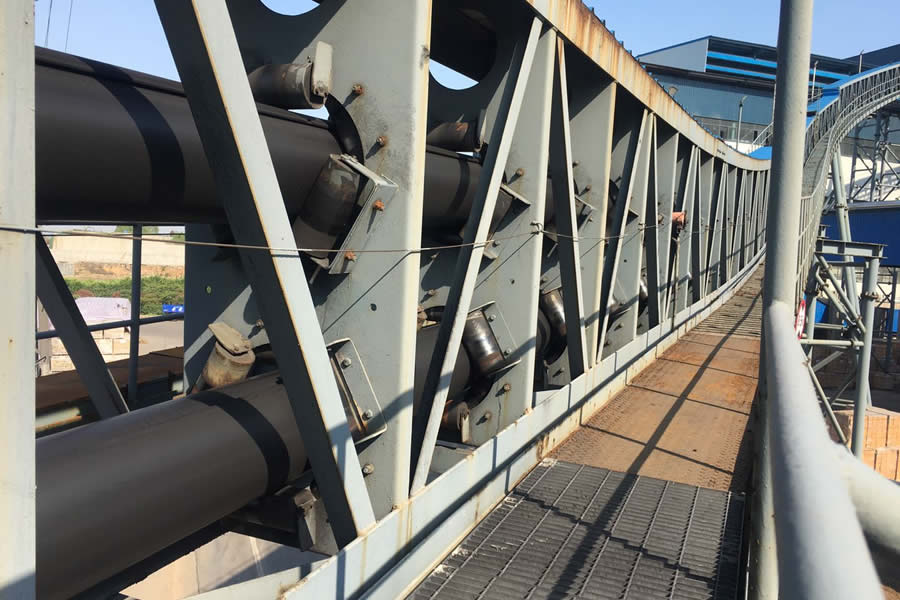
Application
Ports and Terminals
- Bulk Material Handling: At bulk terminals, pipe belt conveyors are used for loading, unloading, and transporting bulk materials such as coal, ore, and grain. For example, after unloading ore from large vessels, the conveyor transports it to storage yards. With its enclosed tubular structure, it prevents spillage and environmental contamination, making it ideal for long-distance transport in complex port layouts with limited space.
- Auxiliary Conveying at Container Terminals: Pipe belt conveyors can also be used to transport auxiliary materials such as lubricants or spare parts for cargo handling equipment. For small batches of bulk materials requiring internal transfer within the terminal, the system provides an efficient conveying solution.
Mining Industry
- Ore Transport: In mining operations, pipe belt conveyors move extracted ore from mining sites to processing plants or stockpiles. With the ability to navigate challenging terrains, such as slopes and curves, they are especially useful in mountainous mines—reducing the need for road construction.
- Tailings Disposal: The system is also ideal for transporting tailings to designated storage areas. Its enclosed design prevents leakage during transport, protecting soil and water resources from contamination.
Chemical Industry
- Raw Material Handling: Chemical production often involves powdery, granular, or lumpy materials. The enclosed design of the pipe conveyor prevents contamination, moisture absorption, and leakage—safeguarding both the materials and workers.
- Product Conveying: Pipe conveyors also transport finished chemical products—such as fine chemicals or pharmaceutical intermediates—to packaging or storage areas. The sealed structure maintains product purity and quality during handling.
Building Materials Industry
- Cement Production: In cement plants, the conveyor handles both raw materials (e.g., limestone, clay, iron powder) and finished cement. Its enclosed structure minimizes dust emission during raw material transport and ensures smooth delivery of finished cement to packaging or bulk loading stations.
- Other Building Materials: Also suitable for transporting construction sand, gypsum, and other bulk materials.
Power Industry
- Fuel Transport: In thermal power plants, pipe belt conveyors transport coal and other fuels. The enclosed structure reduces dust emissions, protects the environment, and prevents material loss—ensuring maximum fuel efficiency.
- Ash and Slag Handling: The system also conveys ash by-products such as fly ash and slag to disposal or recycling sites, promoting cleaner and more efficient waste management.
Food Processing Industry
- Grain Transport: In grain processing facilities, pipe conveyors move wheat, rice, corn, and other grains. The enclosed belt prevents contamination and product loss, ensuring hygiene and efficiency.
- Food Ingredients and Finished Products: Ideal for conveying food-grade materials (e.g., sugar, salt, flour) and finished goods (e.g., biscuits, chips). The enclosed design meets hygiene standards and protects products during transport.
Advantages
Enclosed Conveying for Environmental Protection & Product Integrity
- Environmental Benefits: The pipe-shaped belt fully encloses the material during transport, preventing leakage and dust emissions. For powdery or fine-grained materials (e.g., cement, flour, coal dust), this greatly reduces environmental pollution and health risks for workers.
- Material Protection: The closed system also protects sensitive materials from moisture, oxidation, or contamination. Ideal for fine chemicals, food ingredients, and other products requiring a controlled transport environment.
Excellent Spatial Adaptability
- Flexible Routing: The pipe belt conveyor supports complex three-dimensional layouts, including horizontal curves (up to or beyond 90°) and vertical bends (uphill or downhill conveying with inclines of 30°–40°). This makes it highly suitable for mountainous terrain, confined factory layouts, and sites with limited space.
- Compact Design: Compared to traditional flat conveyors, pipe conveyors require less space for the same throughput. This is particularly advantageous in space-constrained ports, plants, and urban installations.
High Conveying Efficiency
- Stable Speed Control: Driven by motors and gear reducers, the system maintains consistent belt speed, typically adjustable between 0.8–4.0 m/s, depending on material type and transport requirements—ensuring timely and efficient delivery.
- Large Throughput Capacity: Throughput is influenced by pipe diameter, belt speed, and material bulk density. For example, a pipe with a 0.5m diameter running at 3m/s can deliver several hundred tons of coal per hour.
Extended Belt Life
- Uniform Load Distribution: When formed into a tube, the conveyor belt distributes the load evenly across its circumference. This reduces localized stress, minimizing wear and tear—especially useful for heavy or abrasive materials like ore.
- Protection from External Damage: The enclosed structure shields the belt from sunlight, rain, and sharp objects, particularly important for outdoor operations. This protection reduces belt replacement frequency and lowers maintenance costs.
Operational Reliability
Stable Performance: The uniform material distribution and tubular design offer excellent balance and stability. Even on curved or inclined paths, the belt resists misalignment and maintains consistent performance, ensuring uninterrupted production.
Minimal Spillage Risk: Since materials are enclosed within the belt, the risk of spillage is virtually eliminated—critical for handling hazardous chemicals or food products. This also reduces material waste and improves workplace safety.
Technical Specifications
Pipe Belt Conveyor | ||
Conveying Capacity | 500 – 800t/h | Customizable |
Pipe Diameter | 150 – 300mm、300 – 600mm | |
Belt Speed | 0.8 – 4.0m/s | |
Operating Temperature | – 25℃~40℃ | |
Bending Radius | 90 – 180m | |
Drive Power | 55-220kw |
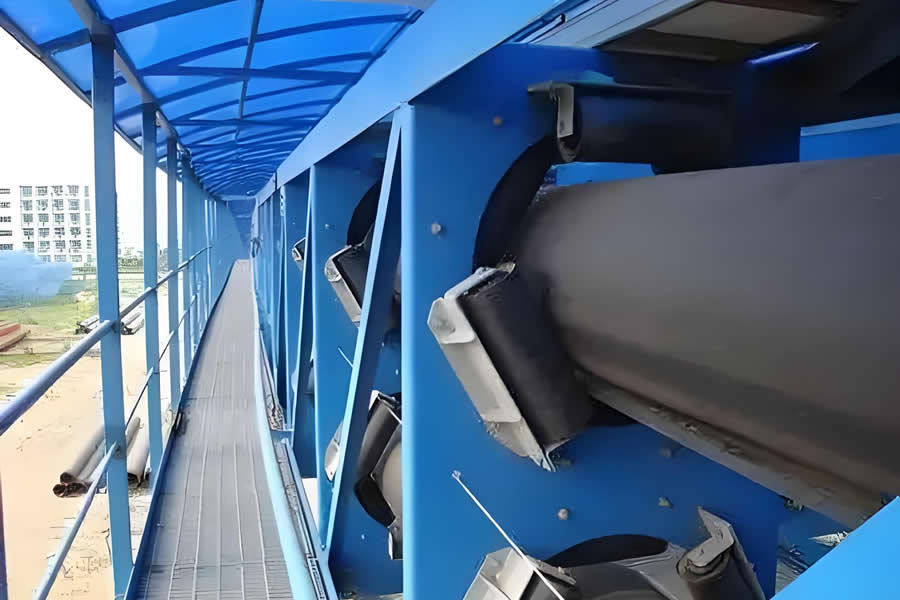
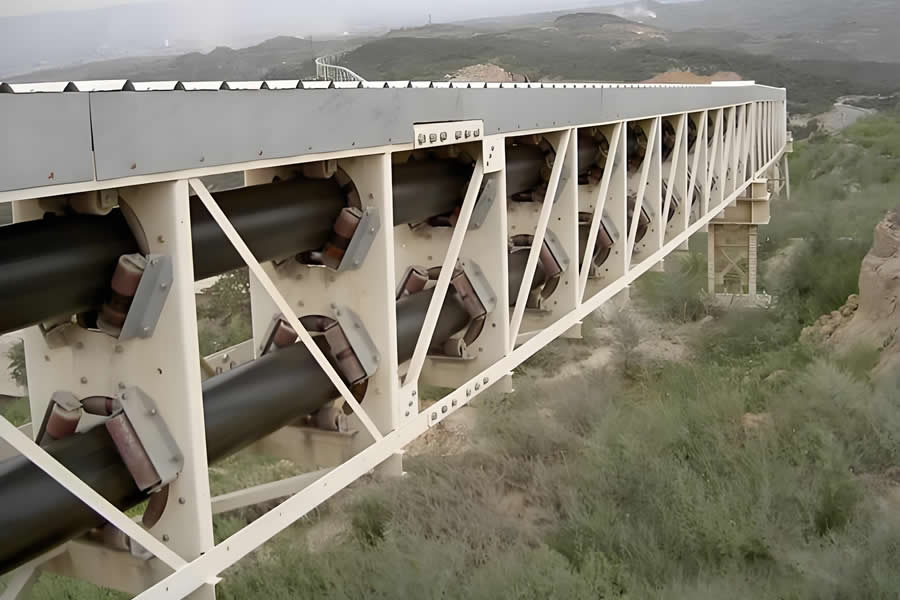
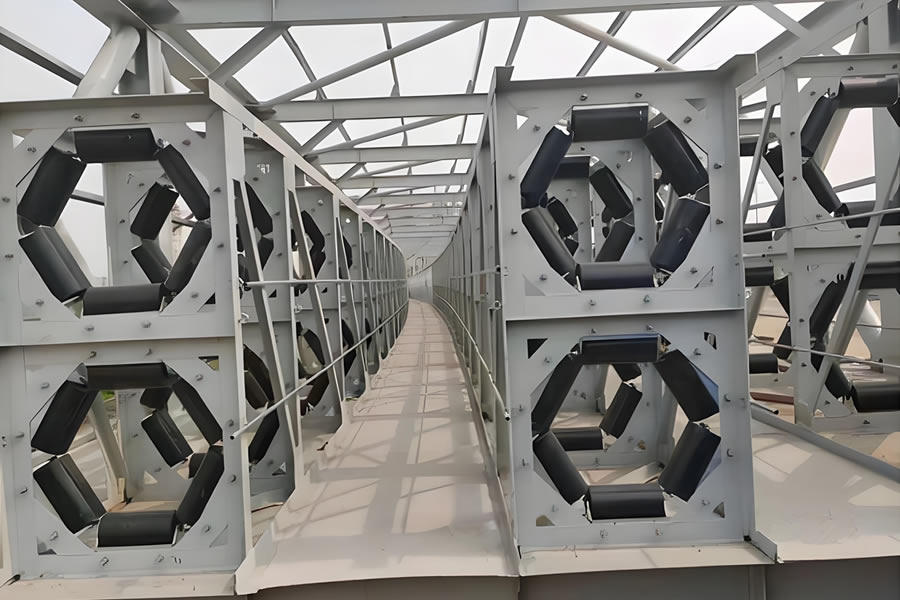
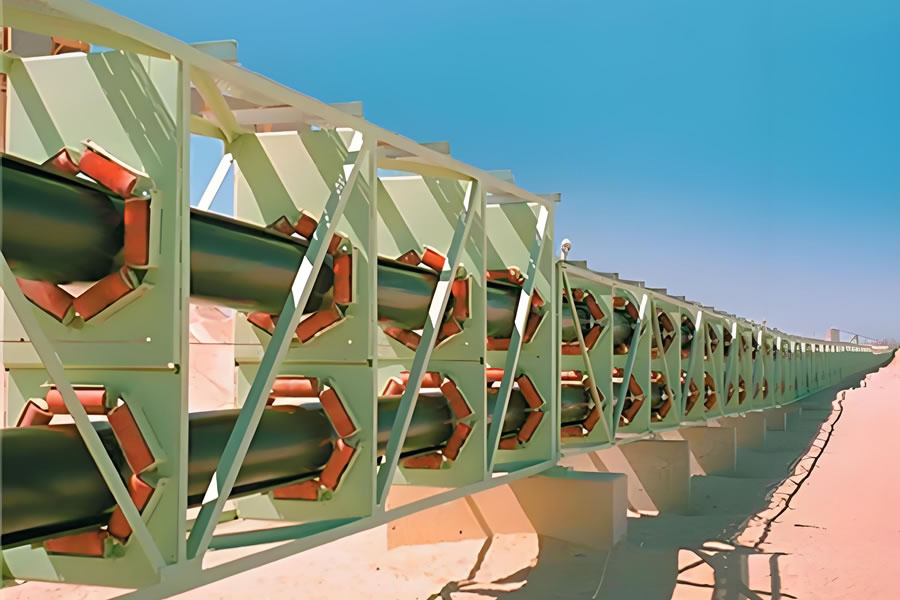
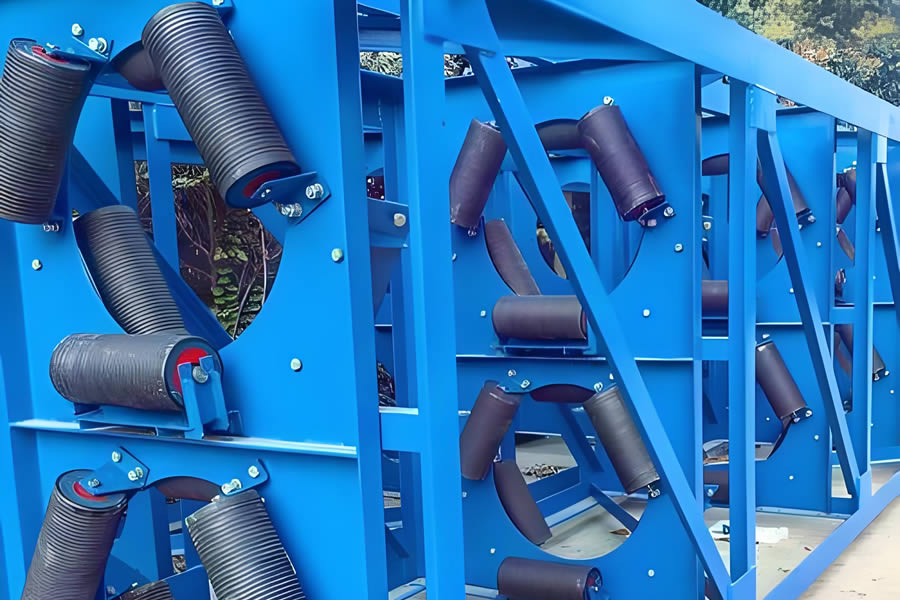
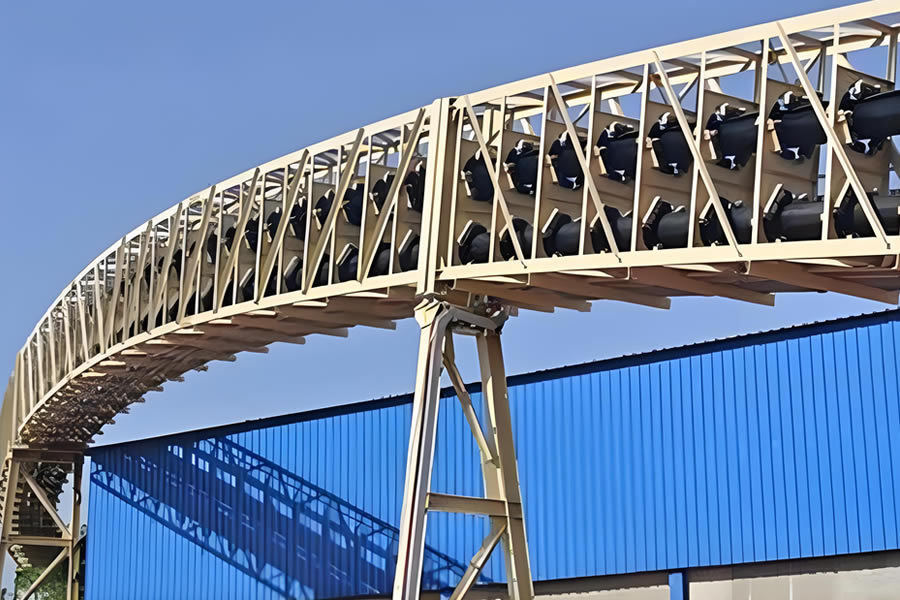