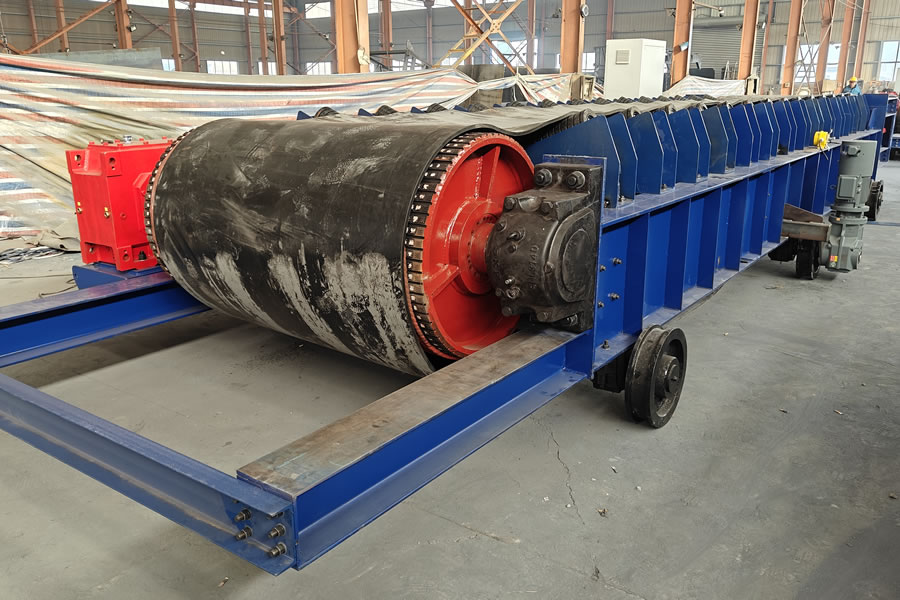
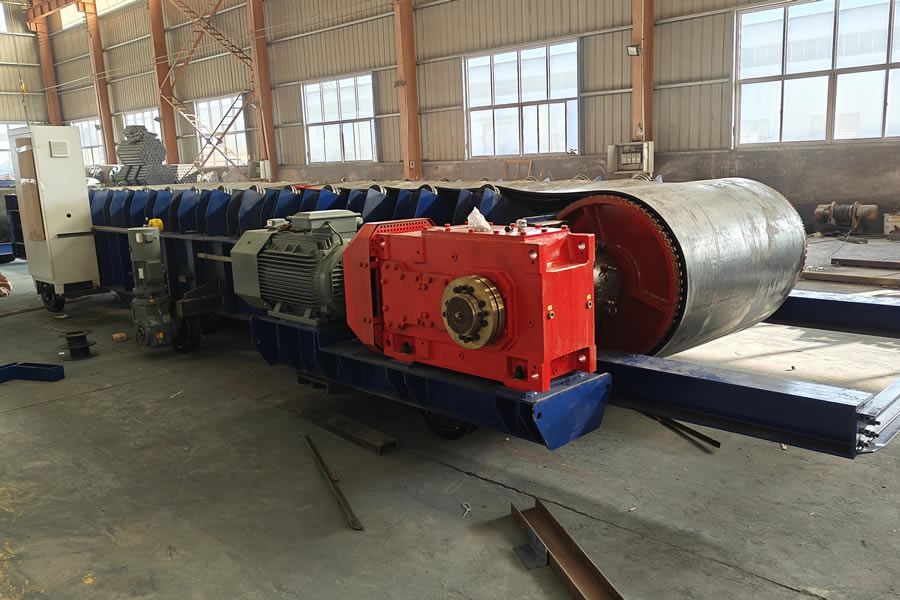
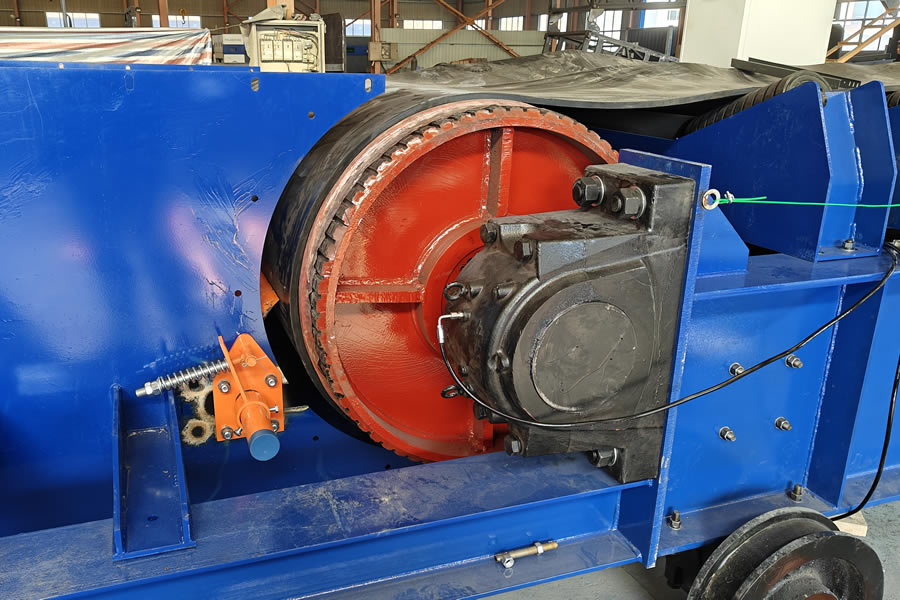
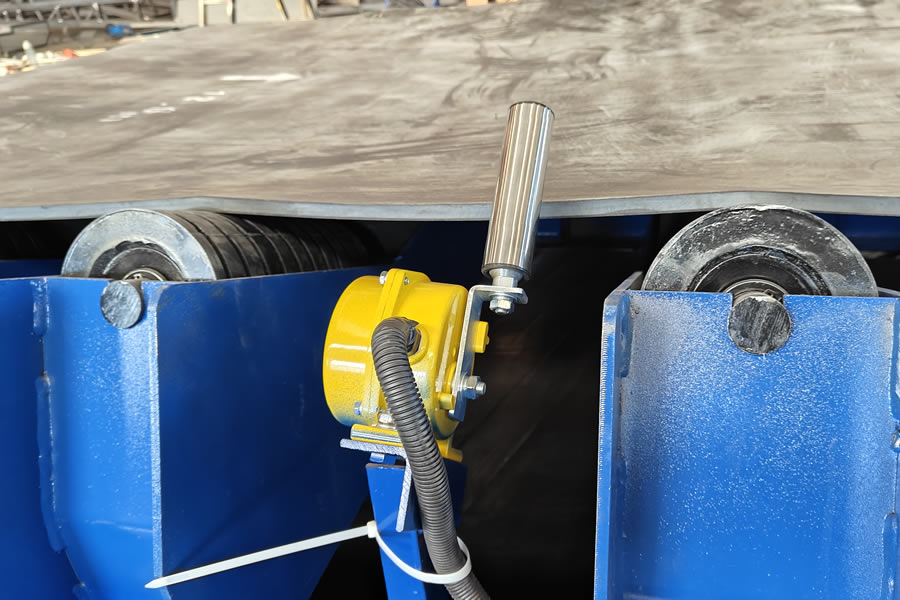
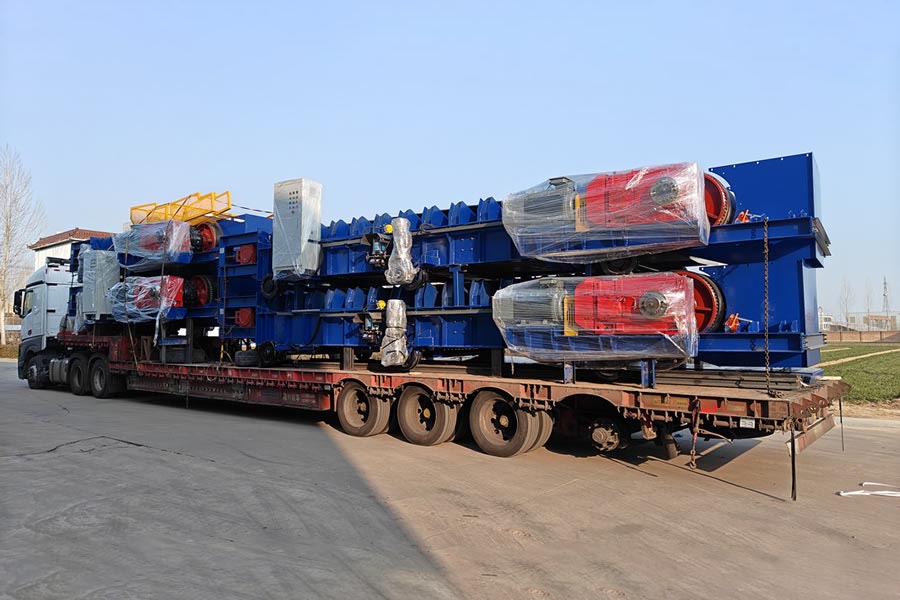
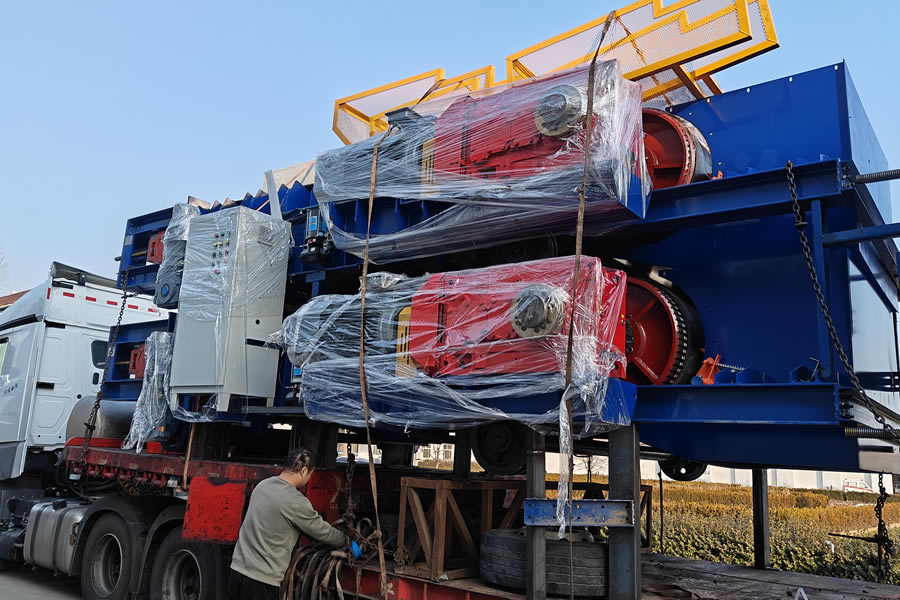
Application
1. Mining Industry
- Ore Extraction and Processing: During the mining process, feeders are used to transport raw ores extracted from the mine to the primary crusher. For example, in large open-pit iron mines, ores of various sizes are conveyed by vibrating feeders at a controlled speed and flow to jaw crushers for coarse crushing. This helps optimize the crusher’s performance and prevents blockages or excessive wear due to uneven feeding.
- Ore Dressing Operations: In ore processing plants, feeders play a crucial role in different stages of mineral processing. For instance, before flotation, feeders deliver crushed and ground slurry evenly to the flotation cells, ensuring effective contact between valuable mineral particles and reagents to improve separation efficiency.
2. Building Materials Industry
- Cement Production: Feeders are essential throughout the cement production process—from raw material extraction to final packaging. During the raw material feeding phase (e.g., limestone, clay), belt feeders precisely control the feed rate into the raw mill. In the packaging phase, screw feeders accurately dose cement into bags by weight, ensuring product consistency.
- Sand and Gravel Production: In aggregate production lines, vibrating feeders are used to transport raw stone from stockpiles to crushers. Since different sizes of finished materials are needed, feeders work with screening equipment to adjust the feeding rate according to particle size and production requirements, ensuring compliance with standards.
3. Chemical Industry
- Fertilizer Manufacturing: Accurate raw material feeding is essential in fertilizer production. In compound fertilizer plants, multiple materials must be blended according to specific formulas. Loss-in-weight feeders can precisely control the feed rate of each component to meet nutrient ratio requirements.
- Plastic Production: In plastic pellet production, feeders deliver raw plastic materials to extruders or injection molding machines. For high-precision plastic products, such as automotive parts, feeders ensure accurate proportions of multiple plastic resins and additives to meet performance and quality standards.
4. Metallurgical Industry
- Ironmaking and Steelmaking: Feeders deliver iron ore, coke, and limestone to blast furnaces based on precise ratios. For instance, a large blast furnace may require several thousand tons of raw materials daily. Belt feeders integrated with batching systems ensure stable, accurate raw material feeding for efficient furnace operation. In steelmaking, feeders are used to feed alloying elements into furnaces to achieve desired chemical compositions.
5. Coal Industry
Coal Mining and Preparation: In underground coal mining, feeders transport coal extracted by shearers to scraper conveyors and other transfer equipment. In coal preparation plants, feeders deliver raw coal evenly to washing and separation systems.
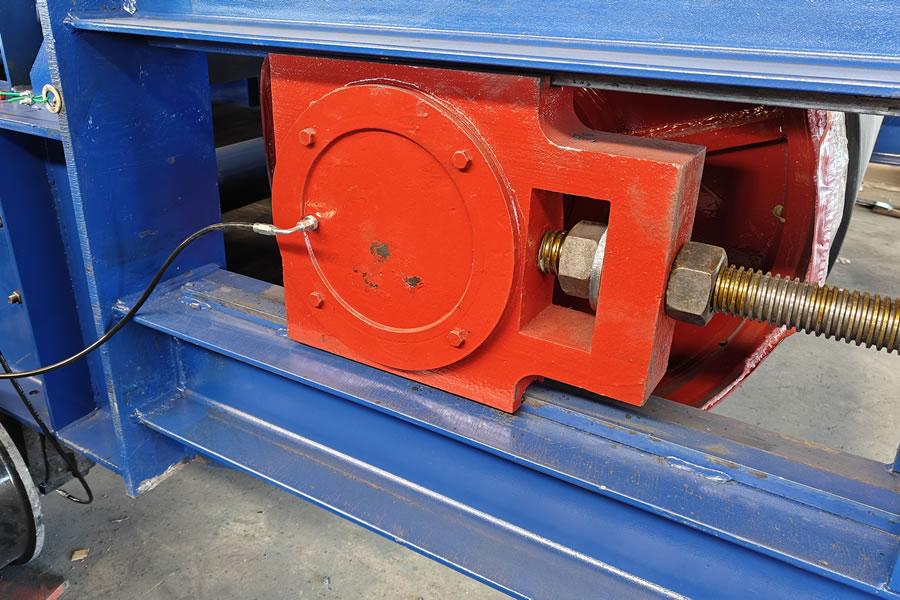
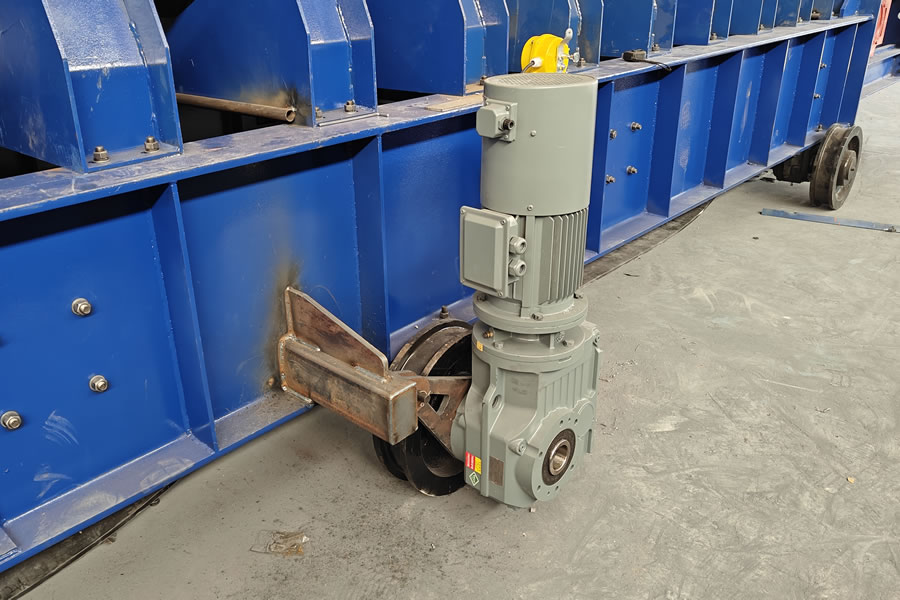
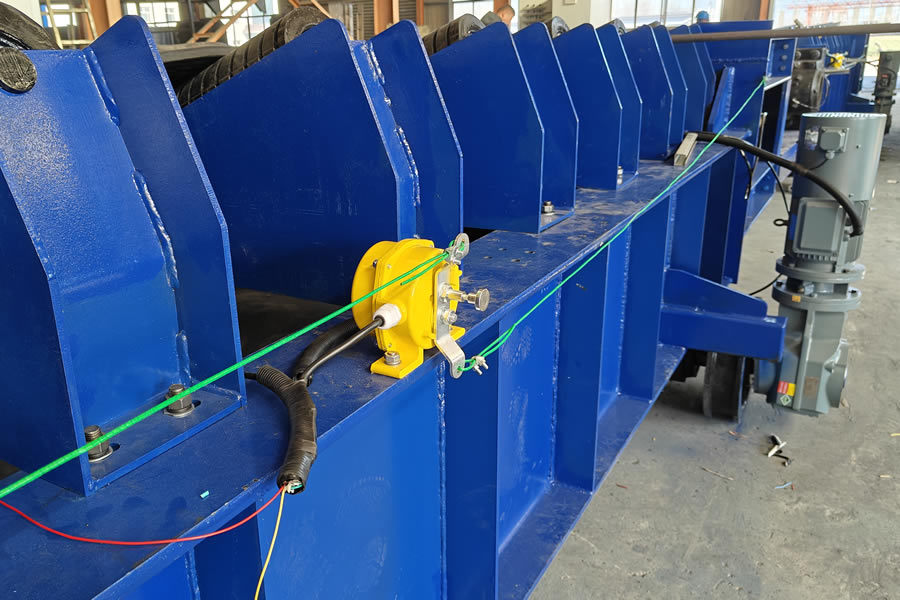
Advantages:
Feeding Capacity
- Many feeders feature high-precision feed control. For example, loss-in-weight feeders continuously measure changes in hopper weight to control feed rate accurately across a wide range—critical for chemical and pharmaceutical applications.
- Electromagnetic vibratory feeders allow feed rate adjustment by varying frequency and amplitude, ideal for processes such as grain milling where precise supply is necessary.
Material Versatility
- Feeders handle a wide range of materials—from large chunks of ore and coal to powdered materials like cement and pharmaceuticals, and granular materials like plastic pellets and grain.
- Belt feeders are suitable for transporting coarse materials like limestone, while screw feeders excel with powders and granules, offering accurate mixing and handling even for slightly moist materials.
Uniform Feeding
- Vibrating feeders use motors to generate controlled vibrations, moving material uniformly across the tray, preventing clogging and overloading.
- Disc feeders rotate to form a stable material layer, dispensing evenly via scrapers—especially useful in blast furnace applications.
Adjustable Feeding Speed
- Most feeders offer adjustable feed rates. Belt feeders change speed by adjusting belt velocity—ideal in coal mining where output fluctuates.
- Electromagnetic feeders vary coil current to fine-tune vibration for precise speed control, beneficial in food processing.
Simple Structure
- Many feeders, like vibrating feeders, have a straightforward structure—tray, motor, springs—making them easy to maintain, even in harsh environments.
- Belt feeders include a conveyor belt, rollers, and drive units, all of which are easy to service for continuous use in aggregates production.
High Automation (for some models)
In grain logistics, automated feeders connected to warehouse systems start, stop, and regulate flow automatically based on order needs, enhancing operational efficiency.
Smart feeders integrate with automation systems. In chemical and pharmaceutical production, sensors monitor flow rate and weight in real-time, enabling dynamic control based on preset process parameters.
Technical Specifications
Feeder | ||
Ore Density | 2000 – 8000kg/m³ | Customizable |
Plastic Pellet Density | 900 – 1500kg/m³ | |
Material Moisture | 1% – 3% | |
Feed Rate Range | 0.1–10 m³/hour | |
Trough Inclination (select feeders) | 0 – 30° | |
Flow Control Range | 0.1kg/h-5000kg/h | |
Flow Accuracy | ±0.5% – ±2% | |
Voltage | 380V 220V | |
Hopper Capacity | 30m³ |