Application
Port and Terminal Industry
- Bulk Material Stockpiling
Crawler mobile stackers play a vital role at bulk cargo terminals. For materials such as coal, ore, and grain, the stacker can move flexibly across the yard to neatly pile materials unloaded from ships or transport vehicles. For example, at a coal terminal, the stacker forms coal piles according to layout and inventory needs, optimizing space utilization and facilitating future reclaiming operations. - Material Transfer
Ports serve as important hubs for multimodal transport. After materials are offloaded from vessels, stackers can store them temporarily before they are transported inland by trucks or trains. Conversely, incoming materials can be stockpiled and later loaded onto ships. The stacker adjusts its position to support various transfer and storage operations efficiently.
Mining Industry
- Ore Stockpiling
In mining operations, especially near processing plants and ore yards, crawler stackers handle the stockpiling of mined materials. After initial processing, ores of different grades or sizes are stored separately. For example, in a copper mine, high-grade and low-grade ores can be stacked in designated areas to streamline further processing and logistics. - Tailings Management
Stackers also support the proper handling of tailings. They help distribute tailings evenly across designated storage areas, minimizing pressure build-up and supporting the long-term stability of tailings dams.
Construction Materials Industry
- Aggregate Stockpiling
Crawler stackers are essential at sand and gravel sites. They stack materials from river dredging, mining, or quarrying, separating coarse sand, fine sand, and different grades of gravel. This facilitates quick access by loaders and ensures efficient supply for concrete plants and other construction needs. - Auxiliary Cement Handling
While cement is mainly stored in silos, smaller cement plants or transfer stations sometimes use crawler stackers for temporary stockpiling. The stacker can place cement bags or bulk material in dry, ventilated locations while maintaining optimal pile shapes to prevent moisture damage.
Chemical Raw Material Industry
- Raw Material Storage
Chemical plants require large volumes of bulk raw materials. Crawler mobile stackers efficiently stack materials like fertilizer components or plastic resins based on their moisture sensitivity or corrosiveness. This helps prevent contamination and ensures clean, organized storage. - Finished Product Stacking
For products like fertilizer or plastic pellets, stackers arrange different batches by specification or order schedule, making warehousing and shipment smoother.
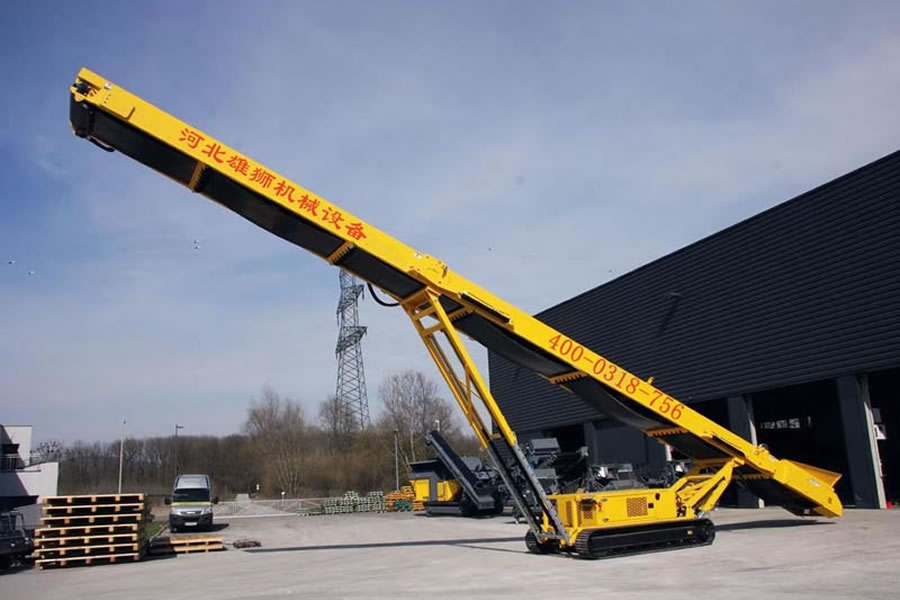
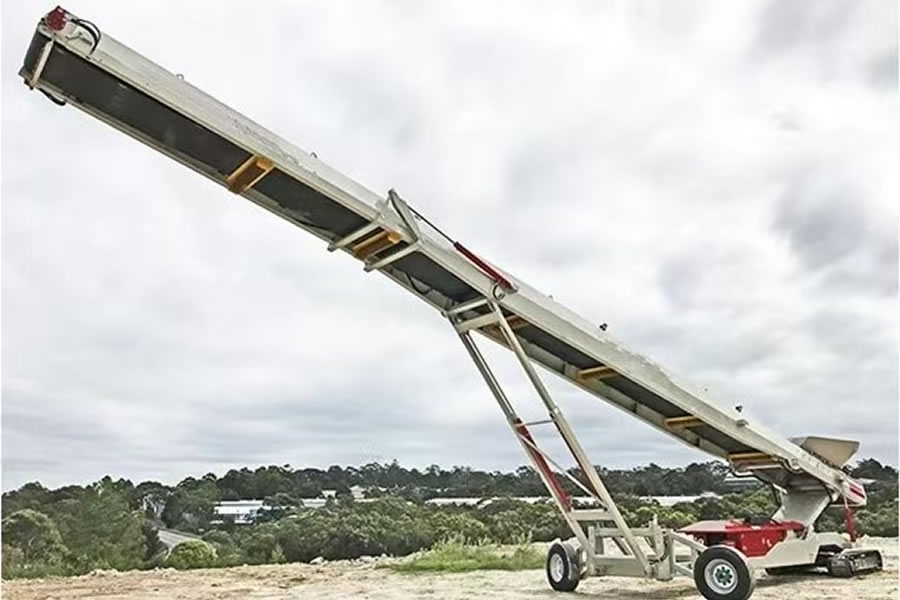
Features and Advantages
Excellent Mobility
- Crawler Track System
The crawler design provides superior traction and lower ground pressure, enabling the stacker to operate on soft, uneven, or rough terrain such as coal yards, sandy soil, or unpaved mine stockpiles. Unlike wheeled machines, it can move steadily even over sunken or irregular ground surfaces. - Flexible Steering and Positioning
Crawler stackers offer exceptional maneuverability, including on-the-spot rotation. This allows precise positioning in tight areas. With positioning systems, the stacker can navigate with centimeter-level accuracy, critical for maximizing yard space efficiency.
Superior Stockpiling Performance
- High Stacking Capacity
Capable of stacking several hundred cubic meters per hour, thanks to efficient conveyor systems and well-engineered discharge mechanisms. Adjustable belt speeds and unloading angles ensure optimal distribution across the stockpile. - Layered Stockpiling Function
Stackers can perform layered stacking, improving pile stability and consistency. For instance, layering coal prevents pile collapse and ensures consistent quality for further processing.
Outstanding Adaptability
- Material Versatility
Crawler stackers handle bulk materials (coal, ore, grain), granules (plastic, fertilizer), and powders (cement). They adapt by adjusting belt speed, conveyor inclination, discharge height, and angle to match material flowability and behavior. - Environmental Compatibility
Built for harsh industrial and coastal environments, these stackers withstand humidity, heat, dust, and salt air. Constructed with anti-corrosion materials, sealed electrical systems, and protective coatings, they deliver reliable operation in ports, mines, and materials yards.
Precise Control System
- Automated Operation
Equipped with advanced automation systems, including sensors for material levels, positioning, and operational status. These systems execute predefined stacking plans—adjusting shape, height, and layer thickness as needed. For example, when a pile reaches its height limit, the system redirects stacking to another area. - Remote Monitoring and Control
Many stackers support remote control via control rooms or mobile devices. Operators can track real-time machine status, monitor pile height, and issue commands remotely.
Reliable Structural Design
- Rugged Frame Construction
Made from high-strength steel with precise engineering, the stacker’s structure withstands high loads and vibrations. Key components like the boom, conveyor, and discharge unit are stress-tested for long-term durability. - Robust Power and Transmission System
Powered by high-capacity engines and supported by gear, chain, or hydraulic transmission systems, crawler stackers ensure steady movement and efficient material handling.
Technical Specifications
Crawler Mobile Stacker | ||
Hopper Volume | 0.5 m³- 5 m³ | Customizable |
Discharge Speed | 1–10 m³/min (customizable) | |
Volume Control Accuracy | ±2% to ±5% | |
Material Size Range | 5–500 mm | |
Material Moisture Range | 0%–30% | |
Discharge Platform Size | 5–10 meters | |
Hopper Volume | 1–20 m³ | |
Installed Power | 585 kW | |
Belt Width | 0.5–2 meters | |
Belt Speed | 0.5–3 m/s | |
Drive Motor Power | 1.5–15 kW |