Application
Port Industry
- Bulk Cargo Handling at Terminals
Bucket wheel reclaimers are extensively used at bulk cargo terminals in ports. For example, at coal terminals, they reclaim coal from stockpiles and transfer it to ship loaders or other transportation systems for vessel loading. At ore terminals, they handle materials like iron ore and copper ore, transferring them from stockyards to conveyor belts for processing or transport. Their high reclaiming capacity greatly improves port throughput efficiency and helps reduce vessel turnaround time. - Stockyard Management
In bulk cargo stockyards at ports, bucket wheel reclaimers are used for stacking and reclaiming materials. They can stack materials neatly according to set patterns and accurately reclaim from specific locations when needed. Through automated control systems, these machines execute precise stacking and reclaiming operations, optimizing storage capacity and material turnover efficiency.
Mining Industry
- Material Transfer after Open-Pit Mining
In open-pit mines, extracted ores are typically stockpiled in designated areas. Bucket wheel reclaimers are used to reclaim these ores and transfer them to beneficiation plants or processing facilities. - Tailings Management
Mining operations generate large volumes of tailings. Bucket wheel reclaimers are used for tailings recovery and storage management. When tailings contain valuable components, the reclaimer can transfer them to reprocessing equipment. For long-term storage, the machine stacks tailings in an organized manner, reducing land use and facilitating future reclamation or environmental treatment.
Power Industry
- Coal Supply for Thermal Power Plants
In thermal power plants, bucket wheel reclaimers are critical for the coal supply system. They reclaim coal from stockpiles and deliver it to conveyor systems for further crushing, screening, and processing before reaching the boiler’s coal bunker. Their stable performance ensures a reliable coal supply, meeting the plant’s high demand and supporting continuous power generation.
Steel Industry
- Raw Material Handling at Steel Plants
In raw material yards, bucket wheel reclaimers are used to manage materials such as iron ore and coke. They stack incoming raw materials and reclaim them as needed for ironmaking or steelmaking processes, ensuring timely and accurate supply. - Slag Handling
Steel production generates slag and other by-products. Bucket wheel reclaimers can retrieve reusable slag like blast furnace slag from stockpiles and transfer it to processing units, where it’s converted into construction materials or other useful products.
Building Materials Industry
- Raw Material Reclaiming at Cement Plants
In cement plants, bucket wheel reclaimers are used for reclaiming limestone, clay, and other raw materials. These are transferred from stockpiles to raw mills for grinding and mixing, forming the raw feed for cement production. - Aggregate Stockyard Management
In aggregate yards, reclaimers manage sand and gravel materials. They stack transported or extracted materials and reclaim them as needed for processing or sales. For example, in construction supply chains, bucket wheel reclaimers efficiently retrieve sand and gravel to meet large-scale building project demands.
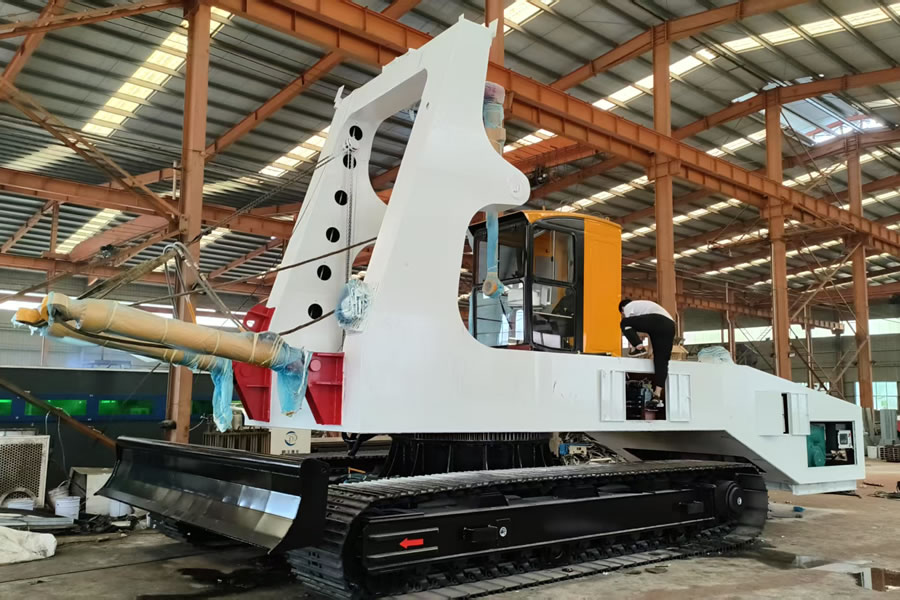
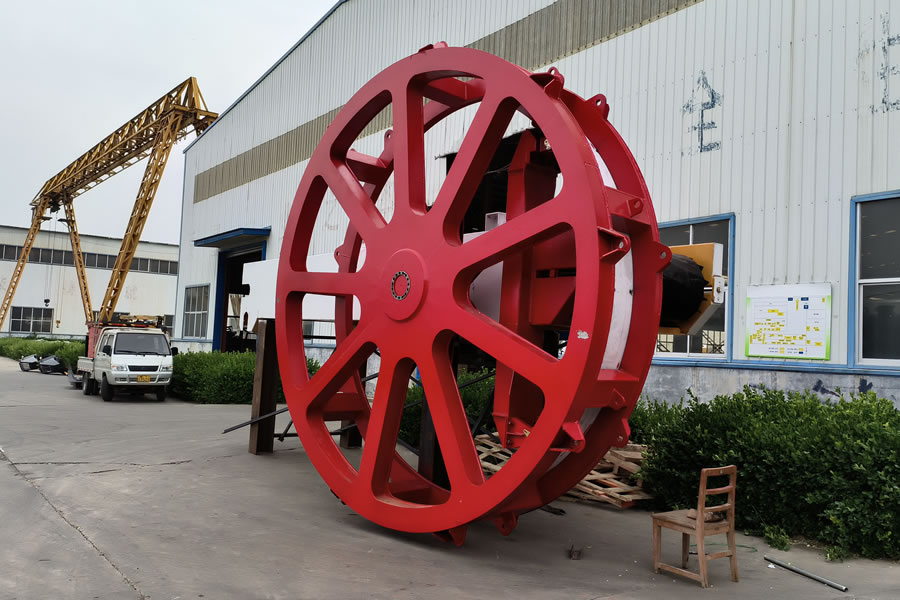
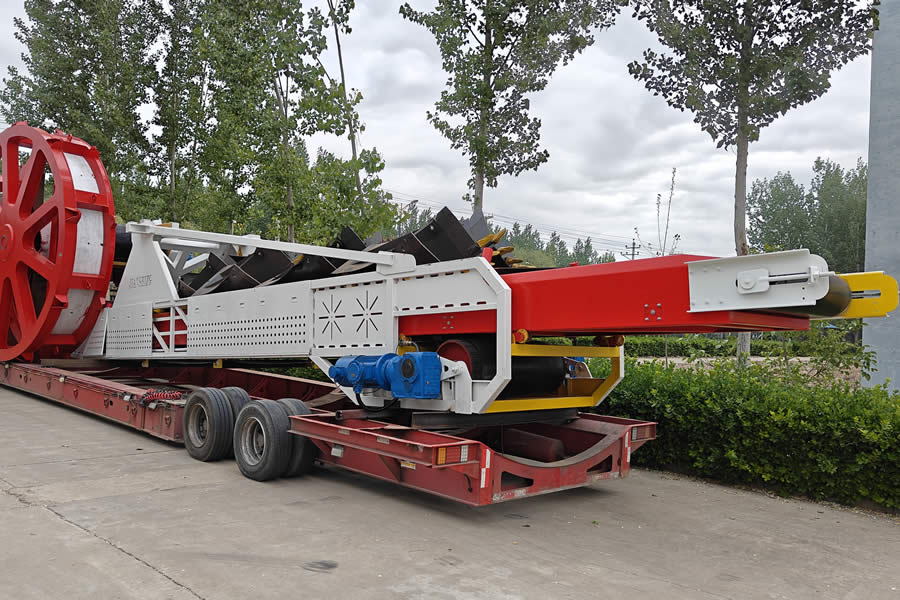
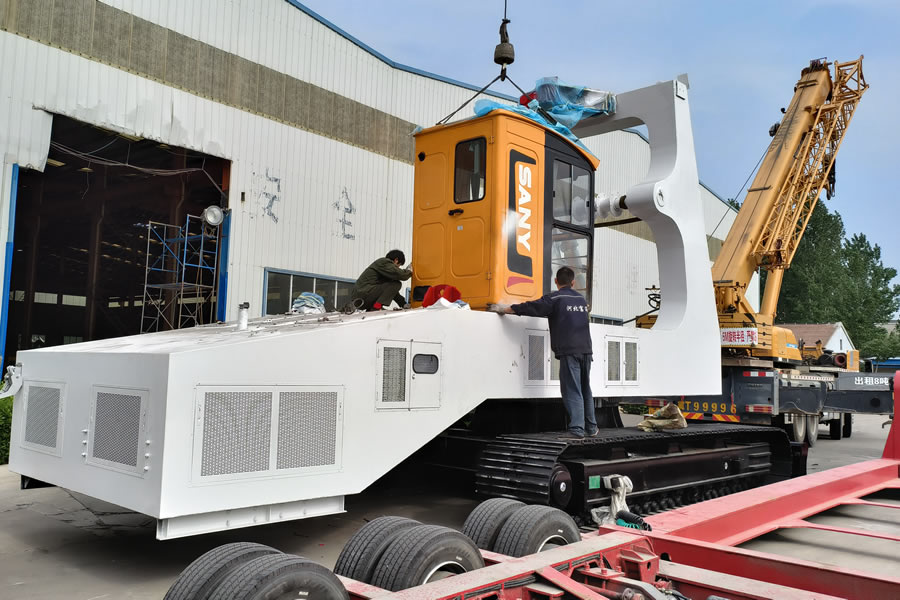
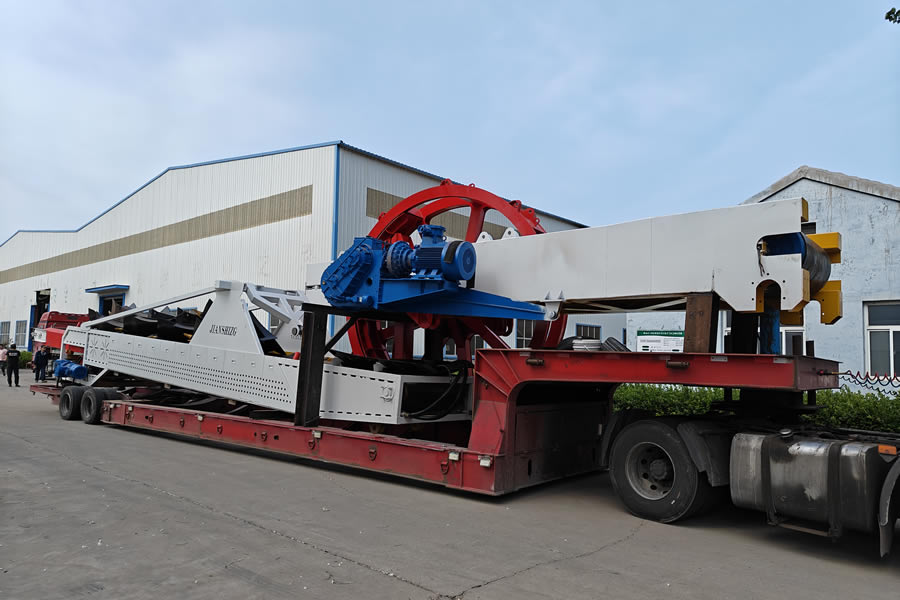
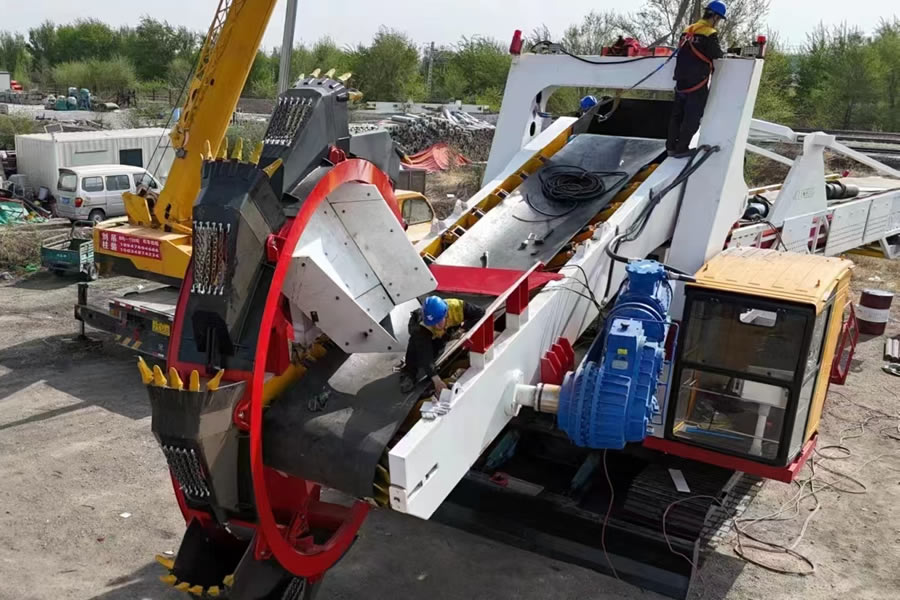
Advantages
Reclaiming Capacity
- High Reclaiming Speed
The bucket wheel design enables continuous material reclaiming. The wheel’s rotational speed can be adjusted depending on working conditions, typically a few revolutions per minute. For example, at large coal stockyards, a bucket wheel reclaimer can handle several thousand tons per hour, greatly improving material throughput. - Large-Capacity Bucket Wheel Design
Each bucket wheel is equipped with multiple buckets designed to maximize reclaiming volume per cycle. As the wheel rotates, the buckets continuously scoop material, minimizing operational downtime and enhancing efficiency.
Reclaiming Control
- Automated Control System
Equipped with advanced automation systems, the reclaimer can perform precise operations. Sensors control wheel position, speed, and reclaiming depth. Operators can input reclaiming parameters via control terminals, and the system executes the operation automatically based on preset paths and depths. - Layered Reclaiming Function
The reclaimer can reclaim materials layer by layer, according to preset thickness levels. This avoids excessive digging or material mixing. For coal and other bulk materials, layered reclaiming ensures uniform grain size and moisture, improving downstream processing or transport quality.
Excellent Adaptability
- Wide Material Compatibility
Bucket wheel reclaimers handle a wide range of materials, including coal, ores, aggregates, and grain. By adjusting wheel speed, bucket design, and operational settings, they accommodate varying particle sizes, moisture content, and material stickiness. For sticky materials, slower wheel speeds prevent clogging; for coarse ores, stronger and larger buckets ensure efficient reclaiming. - Adaptability to Harsh Environments
Designed to operate in extreme conditions, reclaimers function reliably at seaside ports with high humidity and salt exposure, as well as dusty, hot, or cold open-pit mining sites. Their robust structures and protective designs resist wind, rain, dust, and temperature fluctuations, ensuring stable performance on flat port stockyards or sloped mine sites.
Stable Performance
- Robust Mechanical Structure
Built with high-strength steel, bucket wheel reclaimers have a solid and durable frame. Components such as the bucket wheel, boom, and slewing mechanism are engineered for heavy-duty loads. For example, large reclaimers used in ports can support weights of tens to over a hundred tons while maintaining operational stability. - Reliable Power and Drive System
The machines are powered by high-capacity electric motors that drive the wheel, boom movement, and slewing mechanism. Drive systems use precision gears, chains, or belts to minimize mechanical failure and enable long-duration continuous operation.
Environmental Features
- Dust Control
To reduce dust emissions, bucket wheel reclaimers include features such as water spray systems and sealing covers. When handling dusty materials like coal or ore, spray nozzles dampen the material, while covers contain airborne dust—protecting the surrounding environment. - Optimized Energy Use
Modern reclaimers use variable frequency drive (VFD) technology to adjust motor power based on real-time workload. During light-duty operation or idle periods, the system reduces power consumption. Some models also incorporate energy recovery systems that capture and reuse energy generated during braking or downward movement.
Technical Specifications
Bucket Wheel Reclaimer | ||
Hopper Volume | 0.5 m³- 5 m³ | Customizable |
Rated Capacity | 3,000 – 5,000 tons/hour (customizable) | |
Bucket Wheel Diameter | 6 – 10 meters | |
Number of Buckets | 8 – 20 | |
Bucket Volume | 0.5 – 1 cubic meter | |
Slewing Range | 0 – 180 degrees | |
Luffing Angle | –15° to +15° | |
Installed Power | 585 kW | |
Bucket Wheel Speed | 3 – 10 RPM | |
Drive Power | 2,000 – 3,000 kW | |
Power Supply Requirement | 380V – 10,000V |